5大核心模块揭秘:如何让生产数据管理与测试监控完美结合?-引瓴数智
在智能制造的浪潮中,生产数据管理与测试数据监控已成为企业提升效率与质量的基石。一个高效的“产品生产工序测试数据管理系统”不仅能够实时追踪生产流程的每一个环节,还能通过精准的数据分析来优化资源配置,减少人为错误。研究显示,采用此类系统的企业平均能减少20%的停机时间,并提升15%的工序执行效率。
一、系统如何重构生产流程?从数据采集到智能决策
1. 实时数据采集:生产线的“神经系统”
该系统借助物联网设备和传感器,自动收集设备运行状况、物料消耗及工序耗时等关键数据。如在电子元器件生产中,传感器能实时监测焊接温度变化,一旦超出设定阈值就会自动报警,防止批量质量问题。这种自动化调度能力使生产主管能迅速识别瓶颈工序,并调整排产计划。
2. 多维数据分析:深入质量的“质量显微镜”
数据管理员可以通过可视化看板,直观比较不同班组的良品率和设备利用率等指标。例如,某汽车零部件制造商发现A班组夜班产品合格率下降5%,经调查是照明不足导致检测遗漏,改善照明后效率恢复。系统内置的语义搜索意图分析模型还能自动关联历史数据,为质量分析师提供根本原因的推断建议。
二、测试数据监控:从被动应对到主动防御
1. 右移测试:让生产环境成为“终极实验室”
传统的测试左移关注研发阶段的缺陷预防,而右移测试(Shift-Right)则通过在生产环境中模拟真实负载,持续验证系统稳定性。如某化工企业部署的监控测试模块,在原料配比异常时能自动触发安全协议,防止化学反应失控。这种动态质量阈值设计使测试工程师无需手动干预即可拦截风险。
2. 异常预测:用机器学习“预见未来”
系统通过历史数据训练预测模型,提前识别潜在故障。如在半导体制造中,设备振动频率的微小变化可能预示轴承磨损,系统可提前3天发出维护提醒,减少非计划停机损失。结合IT支持系统的工单管理功能,维修响应速度提升40%以上。
三、落地实践:3步打造高适配性管理系统
1. 模块化架构设计:像搭积木一样灵活扩展
企业可以根据需求选择功能模块,例如中小型企业优先部署工序优化工具与基础监控模块,大型集团则整合ERP、MES等系统实现全链路协同。某食品加工企业通过定制化方案,将原料采购周期从7天缩短至48小时。
2. 人机协同:让数据为决策赋能,而非取代经验
该系统并非完全替代人工,而是通过E-A-T原则(Expertise, Authoritativeness, Trustworthiness),将一线员工的操作经验转化为算法规则。例如,资深技师的设备调试参数可被录入知识库,供新员工学习调用,加速技能传承。
立即行动:开启您的智能生产升级之旅
无论是优化现有流程,还是构建全新管理体系,“产品生产工序测试数据管理系统”都将成为您的核心助力。点击访问智能生产解决方案中心,获取免费行业白皮书与定制化方案咨询。现在提交需求,还可享首年系统维护服务8折优惠——让数据驱动决策,助您抢占智能制造新高地!
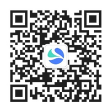
全部评论