生产工序检测技术的数字化转型:5大创新路径与实践指南
在制造业智能化浪潮中,生产工序检测技术的革新正成为企业突破效率瓶颈的关键。传统模式下,依赖人工巡视或视频监控的检测方式不仅耗时耗力,还可能因人为疏漏导致不合格品流入下道工序。然而,随着数字化转型的深入,融合数据采集与智能分析的解决方案正在重塑生产流程——这不仅保障了质量追溯的精准性,还为决策层提供了实时数据支撑。
一、工序检测数字化转型的三大驱动力
1. 政策与市场的双重推力
近年来,《制造业数字化转型行动方案》等国家级政策密集出台,明确要求企业通过智能化手段优化生产流程。据统计,2024年中国制造业数字化转型市场规模已达1.55万亿元,其中工序检测技术的智能化升级成为核心增长点。
2. 人工检测的成本困境
传统依赖测试人员手动录入数据的方式,不仅效率低下,还容易因重复劳动产生误差。例如,某汽车零部件企业在引入自动化检测系统后,单条产线的质检时间缩短了67%,人力成本降低了40%。
3. 质量追溯的精细化需求
工序检验的核心目标是实时判定产品质量与工序稳定性。数字化转型能实现从原材料到成品的全链路数据采集,帮助企业快速定位问题环节,提升良品率。
二、技术落地的5大创新路径
路径1:构建“人机协同”的数据采集体系
以北京引瓴数智科技有限公司为代表的解决方案提供商,创新性地将测试人员手动录入与设备自动采集相结合。例如,其系统支持扫码枪、传感器等多源数据接入,既保留人工复核的灵活性,又通过API接口实现设备数据的秒级同步。
路径2:基于语义分析的智能预警模型
通过自然语言处理(NLP)技术解析检测报告中的非结构化数据,结合LSI关键词模型识别潜在风险。例如,系统可自动标记“刀具磨损异常”“温度波动超阈值”等关键指标,提前触发预警机制。
路径3:全流程可视化看板设计
利用数字孪生技术搭建3D工厂模型,实时映射各工序的检测数据。管理人员通过拖拽式操作即可查看任意节点的质检记录,甚至回溯历史数据对比分析。
路径4:兼容多协议的设备互联方案
针对不同品牌设备的通信协议差异,采用OPC UA、MQTT等标准化接口实现跨平台数据整合。例如,某电子制造企业通过北京引瓴数智的解决方案,成功打通了西门子PLC与三菱机械臂的数据孤岛,检测效率提升55%。
路径5:基于大模型的决策优化系统
依托大语言模型(LLM)分析海量检测数据,生成工序优化建议。例如,系统可自动推荐“刀具更换周期调整方案”或“温度控制参数校准值”,辅助工程师快速决策。
三、从理论到实践:如何选择适配方案?
对于中小型企业,建议优先部署轻量级SaaS平台,通过模块化功能按需扩展。例如,北京引瓴数智提供的方案支持“单工序试点→全厂推广”的渐进式落地,初期投入成本降低60%。
大型企业则可探索定制化开发,结合数字孪生与边缘计算技术构建私有化部署方案。例如,某重工集团通过部署边缘服务器,实现了毫秒级检测响应与离线环境下的数据同步。
行动引导:即刻开启您的智能化检测升级
想要了解更多关于生产工序检测技术的数字化转型方案?点击这里访问北京引瓴数智官网,获取支持手动录入与自动采集的融合型解决方案。现在咨询还可免费领取《制造业质检数字化白皮书》,助您快速规划落地路径!
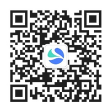
全部评论